Satellite data in PV plant solar sensor quality check
Accurate irradiance data is a key information for assessing the profitability and the performance of solar power plants. Knowing the performance of your power plant, you can perform timely actions to reduce costs and improve results. Additionally, if the performance is poor the Performance Ratio (PR) [1] of the plant can easily drop below a contracted value, resulting in financial penalties.
Typically, ground measurements from solar sensor such as pyranometers or silicon-cells are used to acquire irradiance data, depending on the accuracy required by the project. More than one sensor may be installed [2], both for redundancy and/or to provide representative data for the different conditions (different angles or tilt because of a hillside or due to plants with different designed-sections, surface reflections, micro-climates, dust-accumulation, very large plants). To provide good quality data, all sensors need to be installed precisely, well-maintained (cleaning being very important), and have regular alignment checks and recalibrations. As told before, this kind of maintenance is cost-effective because can avoid financial penalties, but could not always be so feasible, due to other priorities of the O&M staff.
The first question is: when maintenance is really required on that sensor and this maintenance-action is significative?
Another question is: can I use this sensor data to calculate the PR value?
Effective answers are given by satellite-based products: they are an independent, reliable, not-expensive, and “unmanned” source of irradiance data that can be successfully used for checking from remote the status of the sensors, detect those discrepancies that needs urgent actions, or plan for ad-hoc maintenance, using a conditional-monitoring approach saving time and costs.
At i-EM
We developed a satellite-based sensor check able to check the status of the on-site sensors, warning the plant operators when discrepancies from a nominal behaviour are observed, and root causes are suggested, going from simple issues such as data acquisition problems, problems on tilt/azimuth configurations, un–correct offset/scaling of the measurements, to more complex problems such as shading or soiling effects. As a rough estimation of cost reduction, avoiding one day of on-site of local investigation and fault analysis in a plant of about 1 MWp size means saving 500-1000 euros.
Further readings:
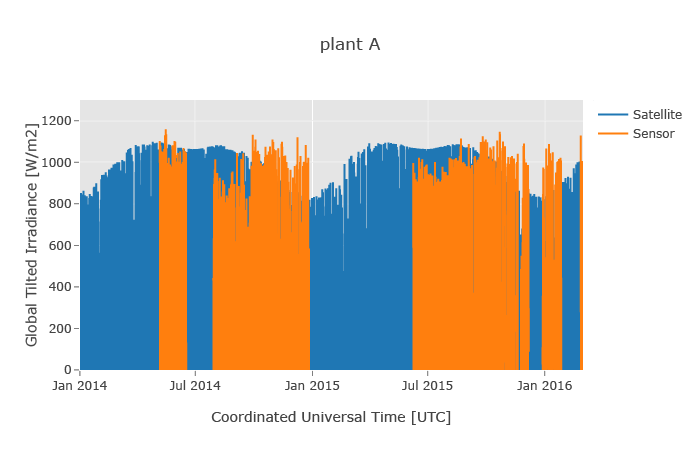
Comparison between sensor and satellite data for a plant A in Italy. This is an example on unreliable data from sensor, as evident from the irradiance on winter periods, compared with the one expected by the satellite-data measurements. This leads to a lower (un-correct) PR value, possibly leading to contract penalties.
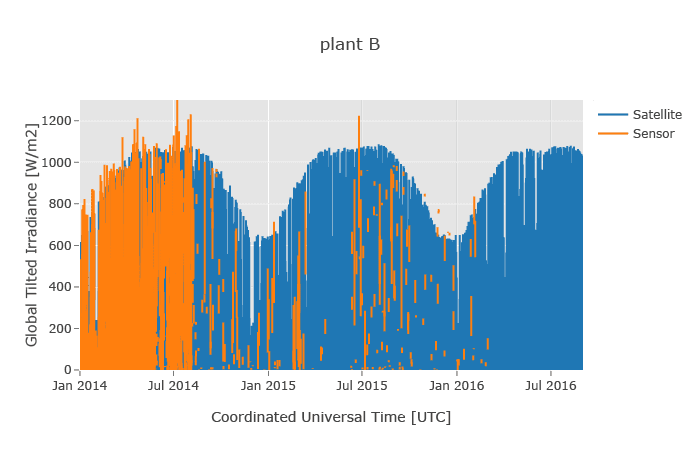
Comparison between sensor and satellite data for a plant B in Italy. This is an example on unreliable data from sensor, with many periods of completely missing data. As a consequence, the PR value is also not reliable.
Notes
[1] PR is the ratio between the system’s final yield and the reference yield. Definition based on [1], in line with IEC 61724-1:2017, and are common practice. (See reference)
[2] Recommendations about the number of sensors to be installed are reported on Internationally accepted guidelines, such as the Project Developer’s Guide, Utility-Scale Solar Photovoltaic Power Plants (IFC 2015) and the standard IEC 61724-1:2017 Photovoltaic System Performance Monitoring. (See reference)
For the curious costumer
At i-EM S.r.l. we have what you need (we hope!)… Try us!
Author
Fabrizio Ruffini, PhD
Senior Data Scientist at i-EM